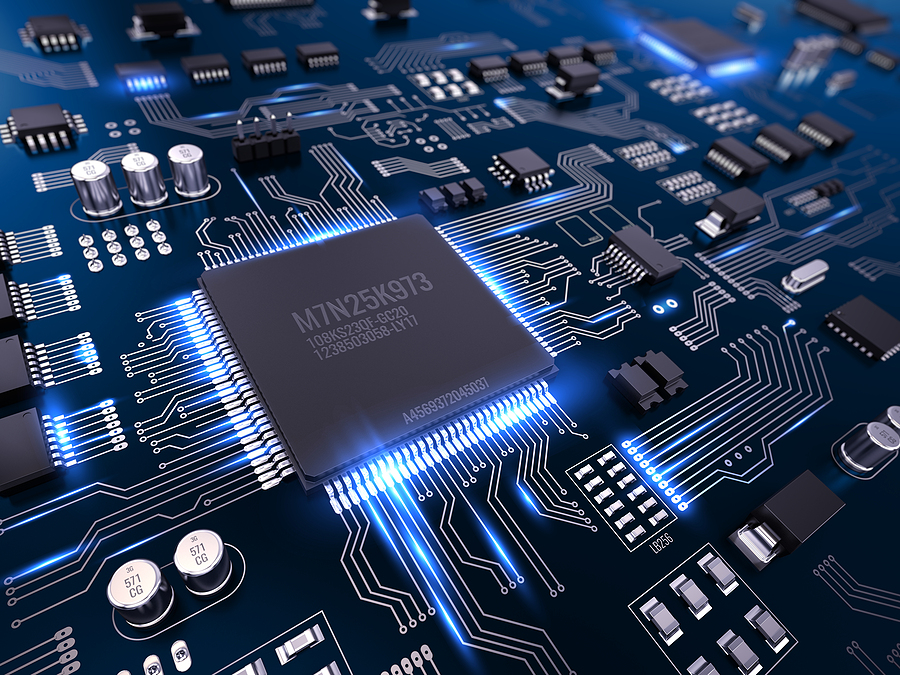
An Alternative Approach
Freshly introduced technology by Garner Products breaks down hard drives in approximately one minute through intense vibration, positioning it as a shredding alternative in asset recovery.
The novel “DiskMantler” has been engineered to handle up to 500 hard drives daily. Its main function involves disassembling a complete hard drive into its key components, which include the printed circuit board, rare earth magnet assembly, hard drive actuator, and drive assembly.
The system also ensures that plastic remains separate from the metals present in circuit boards, which assists in avoiding a mixed waste stream. According to Garner’s chief global development officer, Michael Harstrick, “economic outcomes may vary,” but a greater degree of separation typically leads to increased value recovery.
“If I take the drive and separate the PCB board only, I’ve doubled the value.” He additionally highlighted that the profit margin could be even further increased by detaching the drive assembly and actuator.
Initiating the removal of rare earth magnets involves demagnetizing the drive prior to disassembly, a step that could also significantly enhance the value recovery process. While the market for domestically recycled rare earth magnets is still in its early stages, various federal programs have recognized these resources as “critical materials” with high priority.
In Roseville, California, Garner produces the cutting-edge dismantler at its headquarters. The initial production unit, unveiled for commercial use in late February, marks a significant milestone for the company. As per Harstrick, the DiskMantler offers versatile applications in both ITAD facilities and data centers and allows for installation in any location with a substantial supply of hard drives awaiting processing.
Unique Design Origins
The DiskMantler all started with a request from a client for Garner to design a solution that could detach only the circuit boards, which are often secured with unique screws, from the hard drives located inside data centers.
With the focus of safely removing the component on-site, the engineers at Garner began experiments utilizing vibration to dislodge the part from the drive. They were also careful to avoid manual methods which posed a risk to worker safety and nearby equipment.
This fundamental concept was first introduced by Harstrick, drawing inspiration from the research conducted by German engineer Gerhard Junker. Junker’s exploration into the impact of vibration on bolt integrity paved the way for the establishment of the renowned “Junker test”, a widely recognized technique for assessing bolt self-loosening.
In Garner’s unique approach, engineers delved into the realm of vibration to extract hard drive components, leaving behind traditional industry methods involving robotics. Their solution involved the creation of a compact vibrating device that successfully released the component in as little as 8 seconds at a designated power level.
Then, upon the client’s approval, the engineers opted to conduct an extended vibration test on the hard drive. And unexpectedly, “lo and behold, a minute later, the whole thing came apart,” as Harstrick recounted the incident.
Through extensive experimentation with a range of hard drive brands in the dismantling machine, Garner has achieved meaningful results in effectively processing various drives despite their diverse designs. The key, as Harstrick pointed out, lies in adjusting the dismantling time for each device.
“They still come apart,” Harstrick explained. “It just takes a little bit.”