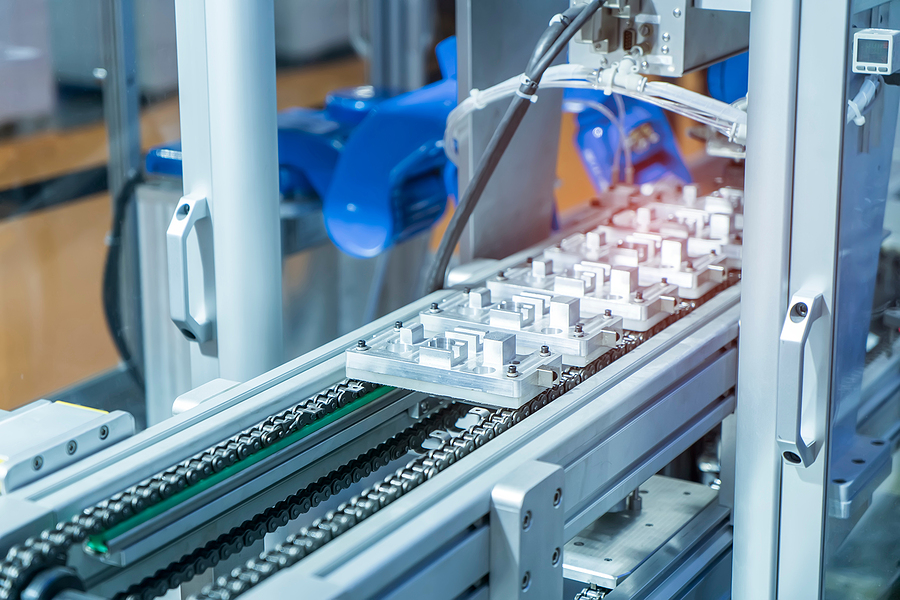
“Industry Leading Processing Efficiency”
With goals of automating its demanufacturing process, Sims Lifecycle Services recently integrated robotic disassembly machinery within its data center decommissioning facilities.
Sims Lifecycle Services (SLS) just revealed the cutting-edge machinery designed by MOLG, a technology company specializing in advanced robotic solutions for the production and dismantling of electronic devices.
SLS has introduced this robotic system to process used hardware from data centers. Over the past few years, the company has strategically focused on data center decommissioning as a key area of its business operations, a decision that has resulted in significant profits for the ITAD provider. With processing facilities established across the United States, SLS is able to offer reliable data center solutions to its clients.
“As our data center clients continue to expand, SLS recognizes the vital role automation will play in keeping pace with our shared growth, and our collaboration with MOLG establishes industry leading processing efficiency,” states Chris Fox, chief operating officer of Sims Lifecycle Services.
When referring to data center decommissioning, the process encompasses retiring IT equipment, carrying out data destruction, and determining whether to refurbish, redeploy, or recycle the assets based on their current state.
The MOLG System
The MOLG system introduces advanced automation capabilities revolutionizing the disassembly and refurbishment of data center equipment. Equipped with robotic arms, it efficiently extracts components from devices, incorporating advanced artificial intelligence and proprietary software to analyze and improve its performance with every device it handles.
Established in 2021, the team at MOLG comprises a wide range of designers, engineers, and various other professionals who have experience in the consumer electronics industry. Then in 2023, MOLG secured financial backing from Closed Loop Partners’ Ventures Group, commending the company for its efforts in “moving the needle on critical mineral recovery through advancing design-for-disassembly and deconstruction.”
Closed Loop commented that it invested in MOLG because, “circularity is at the core of why and how this team operates. They think outside the box of traditional, linear systems, understanding that just because products have always been designed one way, doesn’t mean that process should continue. They are also committed to recapturing as much material as possible––including those previously designed in non-recoverable ways––recognizing that even products lacking optimized designs can be recovered profitably at scale. That’s a circular economy.”
During an interview, Fox emphasized how incorporating robotic technology is crucial for SLS to effectively manage the rapid turnover of equipment in data centers.
“The challenge the industry faces is scale,” Fox stated. “Automation across any industry is there to provide scale.”
Two Worlds Collide
In addition to receiving significant attention from SLS, data centers offer a smoother path for automated demanufacturing compared to the diverse landscape of device types typically seen in traditional electronics recycling processes.
Fox discussed the challenges of managing the influx of materials in the electronics recycling industry, noting that, “you get a lot of material coming in that you don’t necessarily have control of.” In contrast, the data center sector offers a more stable supply of devices. This steady stream will also help to enable MOLG to optimize its demanufacturing processes.
“Automation of demanufacturing is very different than automation of manufacturing,” CEO of MOLG, Rob Lawson-Shanks, expressed to E-Scrap News.
He explained that starting off with data center equipment sets an “infrastructure base of automation” that can be leveraged to enhance the development of automated systems for dismantling devices within the broader ITAD environment.