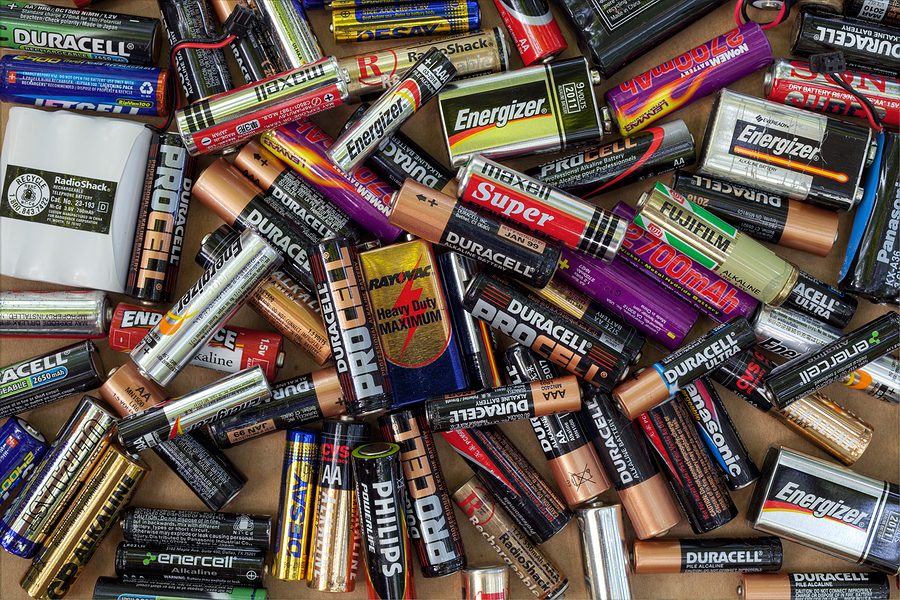
BIDS23
Addressing the challenge of disposing battery-containing devices efficiently, a groundbreaking processing system has been recently created. While it is generally discouraged to send battery-containing devices through shredders for numerous hazardous reasons, the labor-intensive task of manually detaching and securing the batteries before shredding the remaining parts is now simplified due to this new solution.
Introducing the revolutionary BIDS23 Battery-In-Device-Shredder system, Gloyd Recycling Solutions and Archimedes Industry Advisory and Investments (AIAI) joined forces to make a significant breakthrough in the field of recycling. This cutting-edge system, unveiled in December, paves the way for efficient shredding and material sorting of battery-containing devices into three distinct fractions: plastics, metals, and black mass, based on their varying densities.
According to Jeff Gloyd, the founder of Gloyd Recycling Solutions and a valued partner at engineering consulting firm AIAI, instead of manual labor and the potential dangers of handling batteries, this unique system allows facilities to separate them from bulk feedstock. By incorporating a wet shredder and an emissions scrubber, the system guarantees safe shredding, elimination of hazardous gasses, and recovery of valuable commodities.
“I truly believe that something like this can change the status of recycling electronics today,” said Gloyd. “There’s more of this material and there needs to be a solution that reduces risk to facilities and staff and allows warehouses to operate more efficiently. I’m hoping this system can be part of the solution.”
E-Scrap Industry to Benefit
After extensive research and engineering efforts spanning two years, Gloyd expressed the importance of developing BIDS23. The driving force behind its creation stemmed from the urgent need to address a prevalent issue within the e-scrap industry.
The demand for large-scale facilities is primarily driven by the need for high volumes of sorted batteries. These facilities have a specific preference for electric vehicle (EV) batteries that are large in size and contain significant amounts of metals. However, the same cannot be said for the multitude of small-battery-containing consumer devices that make their way into the end-of-life stream. This stream consists of various items such as earbuds, e-cigarettes, toys, and other small electronic devices, which are not as sought after by downstream outlets.
“We’re throwing this stuff away in record numbers, inside record numbers of devices, and that’s where I’ve seen the challenge within our industry,” Gloyd stated.
He pointed out that current battery recycling centers are not receptive to the reduced amount of metals and the inclusion of unwanted battery chemistries and organics in the recycling process of consumer electronics batteries. This presents a challenge for suppliers further up the supply chain as they must search for materials containing batteries, manually extract the batteries from devices, and then sort and package them, with little to no added benefit.
According to Gloyd, there is also a potential risk of catastrophic fires if batteries are stored in large quantities, even if workers diligently remove them from devices with perfect accuracy.
How BIDS23 Functions
Intended for small-scale operations handling quantities of up to 1 ton per hour, the BIDS23 technology incorporates a compact wet shredder as well as a modified water tank to separate the shredded materials into three distinct streams. By utilizing the density differences, the lighter plastics and similar materials float, while the metals (such as steel, aluminum, copper, and circuit boards) sink. Additionally, the shredded batteries transform into a slurry that remains suspended in the water. Then, through a water recirculation system, all three fractions are efficiently recovered.
BIDS23 is also equipped with its own specialized system for controlling emissions, specifically designed to capture any off-gassing that occurs during the battery shredding process.
According to Gloyd’s estimation, it takes either one or one and a half full-time-equivalent employees to operate the BIDS23 system. After securing it in place, plugging it in, and filling it with water, the system, which is delivered via a semi-truck trailer, is ready to be used.
“It’s an incredible value from a plug-and-play perspective,” he explained.
He made an estimation that the lead times, which is the duration from purchase to delivery, are currently around six months.