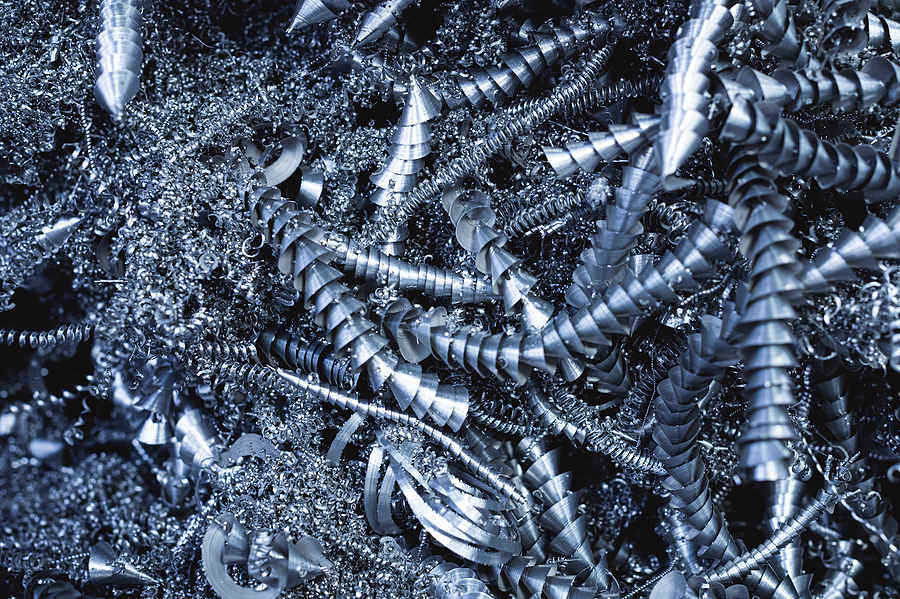
REMADE Forms Partnership
The REMADE Institute has reported that an aluminum firm has started to license an innovative technology to eradicate contaminants from recycled molten aluminum.
An unnamed recycling company has recently been granted access to an advanced aluminum purifying technique as a result of its partnership with Phinix LLC, a REMADE-funded R&D contractor. This technology was developed using resources from the REMADE Institute, an organization which is partially backed by the U.S. Department of Energy.
During a discussion with E-Scrap News, Subodh Das, the CEO of the Clayton, Mo.-based Phinix – spoke about how his company’s technology retrofits existing aluminum recycling furnaces. This specially designed system has enabled the firm to lower impurity levels sufficiently for use within most desired end applications.
A General License Available
Although Phinix has signed a non-disclosure agreement, the company explained that it is still able to provide its technology to other aluminum recyclers via a general license.
“The idea is to diffuse the technology to as many secondary aluminum scrap processors as possible,” he stated.
Phinix has also been part of a venture financially supported by the REMADE Institute, to create technology that can more efficiently reclaim precious metals from e-scrap. This new technology includes the utilization of gas-assisted solvents for extracting metals from printed circuit boards, and Phinix is currently engaged in its licensing process.
“All proprietary process advantages make it more cost-effective to recover precious metals from various electronics wastes destined for landfill. The IP has been exclusively licensed to Phinix, LLC,” a press release stated.
Aluminum Recycling Specifics
Explaining the process of aluminum recycling technology, Das pointed out that while it is possible to obtain pure aluminum for certain specific applications, most commercial uses demand a combination of six different elements: copper, iron, magnesium, manganese, silicon, and zinc. Iron and silicon organically occur in bauxite, which is the natural source of Aluminum, while the other metals are added to obtain certain properties.
However, the combination of alloys found in scrap are not always suitable for use in recycled-content products. Consequently, aluminum recyclers often resort to adding virgin aluminum, which is an expensive and highly carbon intensive process, according to Das.
Patent Process Initiated
Phinix’s new technology is in the process of gaining a patent and its method reduces levels of alloying metals in molten metals to produce recycled aluminum that holds up to the standards of virgin aluminum. The company is continuing to test its technology on various furnaces, with hopes of scaling up its use.
“For us to be useful, we want to try that in all commercially available melting practices,” he explained.
Initiated in 2020, “Selective Recovery of Elements from Molten Aluminum Alloys,” sponsored by REMADE, includes cooperation between several organizations. Spearheaded by Das and guided by REMADE’s tech team, Phinix LLC, Worcester Polytechnic Institute, Kingston Process Metallurgy, Smelter Service Corporation and Certified Flux Solutions LLC are participating in the research project that is still underway.
“With the challenges facing industry today, it is increasingly important to improve U.S. manufacturing competitiveness,” Nabil Nasr, CEO of REMADE, stated. “Our partnership of 100 industry, national laboratory and academic innovators are working together to reduce the energy and environmental burden of domestic manufacturing while delivering value to industry, the economy and the environment.”