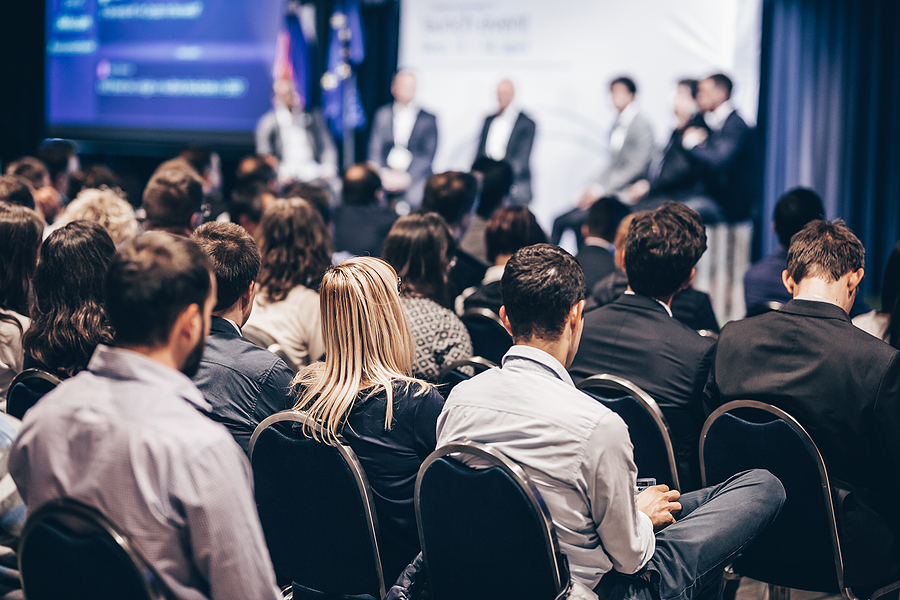
Electric Vehicles Continue to Rise in Popularity
As EV production and sales continue to rise, recycling companies face both potential advantages and difficulties when it comes to collecting rechargeable batteries from these vehicles. Currently, a relatively small amount is obtained at end-of-life stages, but this number is likely to increase in future years.
Recycling practices involving Lithium-ion batteries (LIBs) have become more prevalent as of late, due to the boost in electric vehicle production. Also, in 2021, President Biden declared a goal for 50 percent of all vehicles sold in the U.S. to be zero-emissions by 2030.
Automakers like GM and Ford also announced their own plans to increase EV production capacity. To meet the growing demands of increasing battery production, manufacturers will now look to recycled feedstock as a reliable and cost-effective source, in addition to virgin material sources.
Recycling operations face considerable obstacles regarding reclaiming large-format LIBs from electric vehicles, according to Eric Fredrickson, Call2Recycle’s Vice President of Operations in Atlanta.
“There’s a Venn diagram of compliant and safe,” he explained of handling end-of-life rechargeable batteries. “And you can be compliant without being safe. And you can be safe without being compliant.”
Adding that, “If your organization is struggling with what to do with these batteries and how to do it, then Call2Recycle oftentimes is a great resource for you to better understand the risks associated with what you’re doing.”
At the Recycling Today-hosted inaugural Battery and Critical Metals Recycling Conference in Atlanta, Fredrickson was invited to serve as the moderator for a panel composed of members from across the LIBs value chain.
Recycling as a Focus
“We didn’t really think about recycling until recently,” stated Roger Lin regarding LIB manufacturing. “And it’s been brought on by a big wave of demand for electric vehicles.”
As Vice President of Global Marketing and Government Relations at Ascend Elements, located in Westborough, Massachusetts, it is the responsibility of Lin to oversee operations. The firm applies its Hydro-to-Cathode direct precursor synthesis technology to reusing elements from end-of-life lithium-ion batteries and producing new cathode materials.
Covington, Georgia is home to a recycling center operated by the company. Additionally, an even larger facility is set to be launched in Hopkinsville, Kentucky very shortly. This new operation will be America’s biggest plant for EV battery recycling and engineered materials manufacturing.
When asked what drew him to the company, Lin shared that he highly valued Ascend’s mission to bring recycled materials back into the supply chain and make lithium-ion batteries (LIBs) more sustainable.
Noting the steady rise in electric vehicle battery recycling, Lin attributed it to both economic motives and considerations of supply chain security.
For Derick Corbett, senior vice president of external affairs at Pull-A-Part located in Atlanta, recyclers for automobile parts are serving as “the frontline for EV recovery.” He stated that such mechanisms are already established to provide companies like Ascend Elements with commodities from EVs. “We’re not new to this,” he asserted.
Establishing Processes
As Corbett attested, Pull-A-Part is a giant in the automotive recycling industry. Spanning numerous states, this private company owns and operates 36 yards in 16 states across America.
Once an Electric Vehicle (EV) has reached the end of its usable life, “it is up to us to figure out how to dismantle it and make sure that all of the valuable pieces get somewhere,” he said. “You have to come up with new processes; you have to come up with new procedures. And that’s what the auto recycling industry has been working on over the last couple of years.”
Corbett revealed that the process of stripping down an electric vehicle must begin with properly “powering down” its lithium-ion battery. This step is particularly challenging due to the batteries’ tendency to spontaneously reset. He stated it’s “no easy task.”
For the battery to be detached, a lift must be used so it can be removed. Corbett stated that the battery measures around 6 feet in length and is approximately 1,000 pounds. “And then you have to find a way to store [the battery] safely.”
According to Corbett, the process of recycling an electric vehicle (EV) isn’t drastically different from handling an internal combustion engine (ICE) vehicle. Though, there are some distinctions. As he noted, storage is a concern because, “You can’t just throw the battery next to the rest of the cars because it could explode.”
When shipping batteries, the associated regulations and responsibilities must be respected, he noted. “Your obligations are, when you ship it, it’s hazardous material—it costs a little more money to get it where it’s got to go. You’ve got to be careful not to do it wrong.”
Corbett also highlighted the significance of informing local fire departments and emergency personnel of a facility’s resources, and how to respond in an emergency.
“But once you have established those processes, your costs are very nominal,” he continued.
Utilizing the Shredder
After Pull-A-Part and other similar companies have extracted the valuable parts for reuse and nonferrous metals, they are then sent to an auto shredder for recycling, such as SA Recycling’s facility in Atlanta.
SA Recycling, headquartered in Orange, California, is an established leader in the auto shredding industry. According to Vice President and Regional General Manager, Bobby Triesch, the company has integrated 21 shredders into its system that processes about 1 million cars each year. This includes 300,000 shredded at its Georgia-region operations which are then recycled back into the economy.
Although Triesch noted that many end-of-life vehicles first pass through an automotive parts recycling company, this is not always the case. “For whatever reason, the value of those parts is not enough to have a delta in price for them to get more money selling it to a Pull-A-Part,” he explained.
Though no electric vehicles (EVs) have arrived yet, the Georgia region of SA Recycling has received a few hybrids. “As we go forward, with the trend of having more and more electric vehicles, 10 years from now, five years from now, 20 years from now, certainly it’s going to be different. And you would expect that 20 years from now … there may be electric vehicles that for whatever reason still don’t have enough of a residual value other than to get scrapped out. … [I]f one comes to us, we have to be prepared to be able to safely separate that battery from the rest of the metal and then shred the metal.”
Triesch indicated that at the company’s shredder yard in Atlanta, a hybrid vehicle that was part of a lawsuit was run through the shredder without anyone knowing it was a hybrid. This caused sparks and an incredibly loud sound, but luckily, there were no combustion events.
The OEMs’ Role
Fascinated, Frederick inquired about the function of automotive original equipment manufacturers (OEMs) in the end-of-life process. To this, Corbett responded that at present there is no involvement. “It’s a market-driven commodity.”
Discussing the evolution of OEMs in automotive recycling as the industry shifts to electric vehicles, it was mentioned that such a conversation would take 45 minutes to fully cover. The introduction of extended producer responsibility, or EPR, also came into the discussion adding that some parts of EPR “are really not good.”
“Unfortunately, automakers don’t have a great history of designing for recycling,” Triesch said.
“The OEMs do not plan to manufacture to recycling specifications or needs or requirements or anything to make it easier, but they have always sought to maintain control over the commodities that are in the vehicle; they have always wanted to find a way to close that loop and make sure that they can maintain control of those commodities,” Corbett said. “Batteries are going to be in the same conversation. And you know, auto recyclers, scrap guys, we see the value, we see the free-market-driven recycling industry, and we don’t want to be shut out of that.”
Lin explained that Ascend has made it abundantly clear to battery producers that any difficulty experienced by recyclers or processors while extracting valuable materials from EV batteries will result in a deduction of funds. “we’re going to have to dock you that much money as we process it for you.”
As demonstrated by Triesch, automotive OEMs have an opportunity to incorporate recycling in the design of batteries due to the limited supply of metals and minerals. He commented, “[T]here really is a good chance because it’s in their self-interest to design the power systems and batteries for being able to be as cost-effectively and efficiently recycled as possible.”
Remanufacturing Options
As indicated by Corbett, Pull-A-Part handles electric vehicle (EV) batteries in the same way as other automotive parts, providing lithium ion (LIBs) and nickel-metal-hydride batteries to the auto repair industry. “But lithium-ion batteries and nickel-metal-hydride batteries are unique from car parts because they have a dual function. A lot of the batteries that get resold aren’t resold as auto parts. They’re resold as energy storage units. There’s this whole market out there for these commodities that competes with the recycling market, which is good. But as we focus all of our energy infrastructure on lithium-ion batteries, well, demand is going to do it demand is going to do, and we’re going to have multiple competing partners for these commodities.”
In contrast to lithium-ion batteries (LIB), hybrid electric vehicle battery cells are characterized by lower voltage and lower volatility, thus making them less challenging to refurbish or replace. In the past, LIB packs usually featured a modular design where it was easy to remove and reuse good modules from a recovered pack. By contrast, today’s LIB packs require welding which renders this practice more difficult.
Lin explained that a LIB is full of value, and consequently battery OEMs, auto OEMs and other stakeholders are coming together in the recycling realm to decide how best to manage the worth of these minerals due to the predicted lack of lithium, nickel, and cobalt within the supply chain in future years.
“This whole idea of remanufacturing is a very elegant and excellent idea. It’s all going to come down to the execution of that idea,” he asserted. “Yes, there’s more value in a working battery than there is in shredding it to black mass and extracting elements. … But what about that refurbished battery? Where does it go? Is it being used within originally designed parameters? Was it assembled properly? Are there any issues with the way you’re busing the different cells and modules together? We all know that lithium-ion batteries can be volatile and hazardous. … There are a lot of ways they can go wrong.”
Lin added, “In my perspective, I think reman is interesting. I think if we don’t do it right, there’s going to be problems either from a safety perspective [or] performance perspective, which will likely cause challenges for the players in that market. And then market application will rapidly degrade to third-world countries … and then we go back to supply chain issues. We’re going to see leakage of things like lithium, nickel cobalt that you want to have in this economy.”
According to him, to ensure successful reuse of batteries, manufacturers need to consider this aspect right from the design stage. “If it’s done deliberately, intentionally, again, from the get-go … then you can say that it could be viable, and you might be able to take those battery packs, all strung together, let’s say and then put them in the Georgia power grid.”
A Changing Landscape
Corbett highlighted that remanufacturing EV batteries is the most lucrative endeavor at present. “But the deficit figures for lithium over the next 10 years, and then again over the next 20 and 30 years, are incredible. And, so, the only way to make that deficit up is through Ascend Elements and those like it feeding that feedstock back into the manufacturing chain. And so that demand is going to shift that value structure in a way that tilted toward recycling.”
Although EVs tend to contain less elements and components that auto recyclers, like Pull-A-Part, can gather and resell, Corbett expressed that “there’s still a lot of other good stuff” that can be salvaged and sold.
He concluded, “Smart guys are going to figure out how to work on their own cars. Even though it doesn’t have an engine and a radiator and a four-barrel carburetor, it’s going to have whatever kind of switches and buttons that Tesla or whatever other EV has, and folks can figure out how to buy those parts and pieces and reuse them in the cars that they repair.”