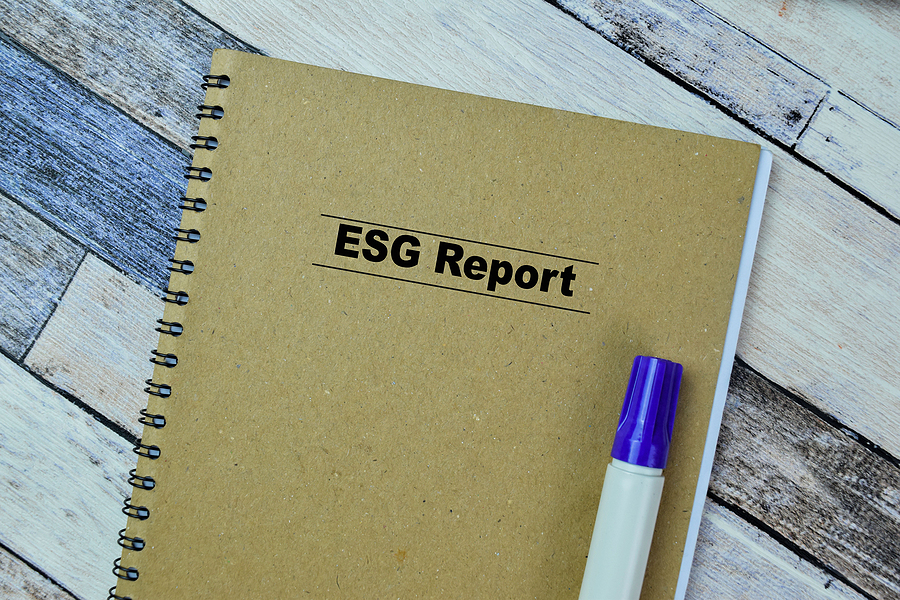
ERI Releases its 2022 ESG Report
ERI’s sustainability report revealed a decrease in the total pounds of electronics handled last year, but a noteworthy increase in the weight of items diverted for reuse.
In its 2022 Environmental, Social and Governance (ESG) report, it was indicated that in comparison to 2021, 121.07 million pounds of electronics were recycled last year, or, showed a 5% decrease. However, it was also noted that 4.10 million pounds of these discarded items were salvaged for reuse, amounting to an 8% surge over last year’s figure.
Based in Fresno, California, it was estimated that ERI recycled a staggering 49.20 million pounds of base metals and 24.90 million pounds of plastic last year. Along with this calculation, 16.70 million pounds of materials containing precious metals like circuit boards were also reclaimed. Additionally, 11 million pounds of glass, and 2.60 million pounds of ‘other recyclables’, such as; lamps, cartridges, and packaging, were processed in its facilities, along with 2.10 million pounds of batteries.
Also in the report, ERI also discussed how, despite disruptions to supply chains due to COVID-19, it was able to recover 650,000 electronic components for reuse in 2022.
Recycling Robots in Action
Another noteworthy aspect of ERI’s report was information about its pioneering recycling robots. As a technological first, these machines are powered by artificial intelligence to sort materials resulting from shredding e-scrap.
At its Fresno, Calif. headquarters, installation of the Super Automated Machine (SAM) was completed in 2019. Developed by Denver-based AMP Robotics, advanced artificial intelligence technology powers this system.
In Fresno, ERI has also launched ERNIE, a self-contained flat-screen dismantling system that stands for Electronic Recyclers Next Innovative Efficiency.
ERI is employing robotics technology to create faster, more efficient processes and to flexibly manage any staffing limitations.
“It took us three years to come up with, but it’s unbeatable,” John Shegerian, ERI’s co-founder and executive chairman told E-Scrap News. “[It’s a] game changer on our commodities.”
SAM’s Capabilities
About six years ago, ERI had the opportunity to collaborate with AMP Robotics. This introduction came through Ron Gonen, co-founder and CEO of Closed Loop Partners, who presented Shegerian to Matanya Horowitz, founder of AMP Robotics in 2014.
Backed by some of the largest names in consumer goods and retail, Closed Loop Partners provides many avenues for investments into greener technologies and circular commerce. One branch of this family of organizations, Closed Loop Ventures, led by Gonen’s group, invested into AMP Robotics.
To create a system capable of sorting e-scrap streams, AMP Robotics and ERI’s engineering team collaborated. This required not only programming its system to recognize shredded material, but also setting up a suction process that was capable of functioning effectively.
As Horowitz revealed to E-Scrap News, SAM is organizing materials discarded from an eddy current separator. It can recognize and categorize printed circuit boards, stainless steel, aluminum, black plastic, brass and copper, capacitors, scrap motors known as ‘meatballs’, wire, and more.
Horowitz divulged that the device can manage 80 selections per minute, and then directs the material into four distinct chutes.
He also explained that one of the most difficult aspects in readying the robot for e-scrap, was creating an efficient and reliable gripper. This task was made more complicated by having to design something capable of securely suctioning pieces that had been crumpled and broken into tiny fragments, much smaller than what is usually found in curbside recycling bins.
After much consideration, the partners decided to forgo mechanical grippers and seek an alternative option. Speed constraints and spacing issues were the two primary considerations. With a mechanical hand, speed is restricted and items need to be kept separate on a conveyor in order to keep them from touching one another, an adjustment that would have taken significant modifications to the production line.
Eventually, after experimenting with various elements, AMP and ERI were able to construct a suction gripper. “We really had to tune all those parameters,” Horowitz remarked.
Details on ERNIE and Beyond
The team of engineers at ERI have additionally created a robotic system capable of recycling LCD screens. ERNIE, is a self-contained unit that breaks down LCD screens and separates materials while also trapping dirt particles in its chamber. In anticipation of CRT devices becoming obsolete, ERI has created ERNIE to address the increasing amount of flat-screen TVs entering the end-of-life stream.
“With steady growth of 10-15 percent per year, we are always looking for innovative ways to enhance efficiencies,” Shegerian stated. “Working with our friends at AMP we developed smart technology that will continue to increase our sorting accuracy as our processing volume increases so we can free up our employees to perform ITAD and data wiping services. We are very proud of SAM and ERNIE and being the first in our industry to incorporate robotics and A.I. into the process.”
The future for ERI continues to be bright as the firm has also recently expanded its presence in the U.S., with the addition of a new facility in Goodyear, Arizona. This brings its total number of processing locations to nine across the country.