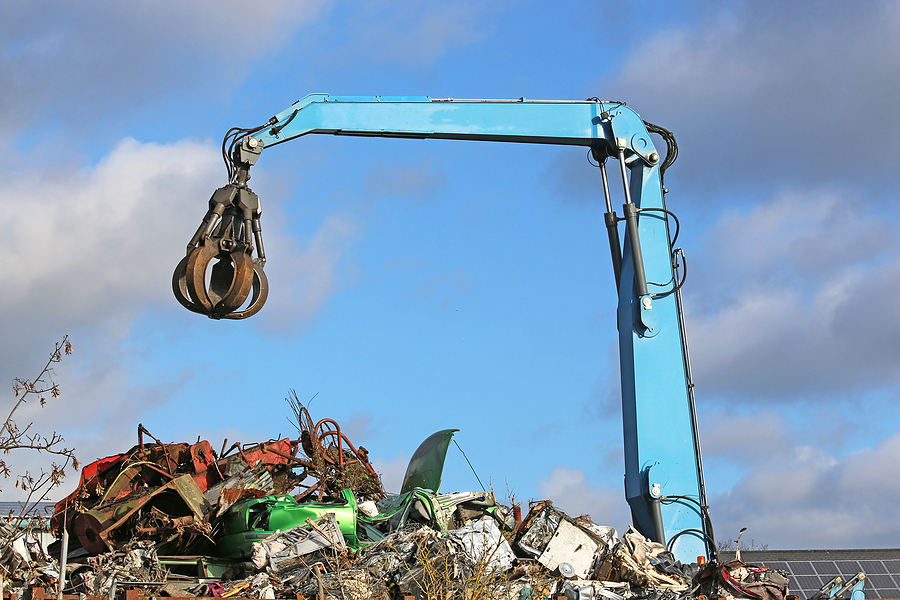
Electrical Material Handlers Rise in Popularity
Though not as commonly used by scrap processors, certain material handling equipment manufacturers have attested to the reliability of using more modern, electrical material handlers. Contrary to popular belief, these machines can provide a similar level of efficiency as their diesel-powered counterparts.
“Electric material handlers have had a very long tradition at [Terex Fuchs], with our first electrically powered equipment being delivered to customers as early as the 1980s,” according to Florian Bender, the Chief of Product Management and Marketing at Terex Corp. based in Norwalk, Connecticut.
Bender recently journeyed to a scrap yard in Germany that is home to an electrically powered machine, which has operated for over 100,000 hours.
“The performance of our electrically powered machines is in no way inferior to that of our diesel-powered variants,” Bender stated. “On the contrary, thanks to the extremely load-stable electric motors combined with the high torques, electric machines offer strong performance in the field.”
Last year, Cimco Resources Inc. from Loves Park, Illinois saw a “strong performance” when the firm implemented an electric scrap handler. The 870 Hybrid material handler was introduced to its Sterling, Illinois scrap yard location. The electric-drive piece of machinery was supplied by a German founded company with its U.S. subsidiaries; Sennebogen LLC located in North Carolina. The addition joins the other six recycling facilities currently operated by Cimco Resources across Illinois.
The Sterling yard has long utilized a diesel-powered crane to feed materials to its Metso auto shredder. Every day, the facility processes up to 800 tons of material, much of which goes through the shredding machine.
“We run multiple products through our shredder, so we have multiple piles of materials around the infeed area,” stated the operations manager at Cimco, Ron Brenny.
An Increase in Productivity
Cimco successfully installed the 220,000-pound 870 Hybrid material handler on a towering 9-foot pedestal. It boasts a 90-foot boom that allows it to reach multiple piles of sorted material without needing repositioning. This semistationary material handler is even outfitted with tracks, allowing for easy transportation around the yard as necessary.
Last year, Brenny acquired the 870 Hybrid and shortly thereafter observed a rise in productivity when operating the shredder. He noticed how swift and efficient the machine operates despite its substantial size. “It’s unbelievably quick, probably as fast as a smaller [material handler],” he says.
Although limited mobility can be a challenge for scrap processors when selecting an electric scrap handler, manufacturers of material handlers assert that they provide viable solutions.
At Virginia-based Liebherr USA Co., product manager of Newport News, Chris Keyes, emphasizes the importance of battery packs or mobility packs for electric models that must traverse a yard.
Having visited a scrap yard in Munich, he saw first-hand the machine’s capacity to increase cycle times when loading onto the shredder. This ability was made possible with the aid of the mobility pack, which allowed the electric models to move around freely in the yard.
According to Colleen Miller, the Sales and National Accounts Manager at Sennebogen LLC, regardless of how extreme the temperature is, electric material handlers will start up without a problem. This isn’t always true of diesel-powered material handlers, as they can struggle to function in extreme temperatures.
“Whether working in northern British Columbia in negative degrees or in Arizona, electric material handlers always run,” Miller explained. “That is an advantage for customers working in extreme conditions—you won’t have issues with ambient temperatures.”
Growing Rates of Implementation
Cimco was among the pioneering scrap processors to incorporate the 870 Hybrid into its day-to-day activities, according to Bender. Although manufacturers of material handlers claim that adoption of these machines has been somewhat sluggish in the United States, Keyes strongly believes that this can be attributed to fear of transitioning.
“An owner of a company that has been very successful for many years working with the same type of machines is naturally reluctant to change in a new system,” he says.
Manufacturers of material handlers anticipate that within the next few years, an increased number of electric models will be introduced in the United States.
“Europe is generally very tech-savvy,” Bender stated. “The development of electric drives is being actively driven primarily by our European customers. Scandinavia, for example, is playing a pioneering role in the field of zero emissions. Government subsidy programs are increasing demand for more environmentally friendly drives and at the same time accelerating technical developments.”
Diesel’s High Price Impacts Electric Purchases
Millar says the prices of diesel in Europe have played a major role in encouraging scrap processors to switch to electric alternatives.
“The cost of diesel is very different in the U.S. than in Europe,” she notes. “Diesel costs four times more in Europe. If you’re paying four times [more] for diesel, you’re going to look at other options. … So, European companies are adopting electric models.”
Brenny notes that the demand for electric-powered material handlers have been on a steady rise within the U.S., though it is not yet at the level of Europe. “While this has not yet reached the same extent as in Europe, we are certain that we will see significantly more electrically powered handling equipment in the U.S. in the future,” he says.
“The only thing I can see why someone would have hesitation is the cost,” he states. “You’re looking at paying almost twice as much [for an electric material handler]. You have to justify why you’re paying that.”
According to Miller, some of Sennebogen’s customers have found ways to make use of grants in order to implement electric equipment into their facilities. Particularly, a customer from the port industry was able to receive a grant from the Environmental Protection Agency which covered 65 percent of the cost for an electric material handler, and completely funded bringing power to the location.
“To think that 65 percent of that project is paid for by the government is an unbelievable victory,” she says.
Although initially more expensive, Brenny claims the 870 Hybrid electric model purchased by Cimco has “more than paid for itself” over the past year. The decision to opt for something electric was based on its superior dependability, and decreased need of maintenance compared to diesel models, resulting in significantly less downtime.
In comparison to diesel, Brenny suggests that electric machines provide a much higher mobility and require less maintenance. He explains that they remain “almost maintenance-free compared with diesel.”
“With the cost savings in maintenance, we feel the electric model basically paid for itself in that way,” he concluded.