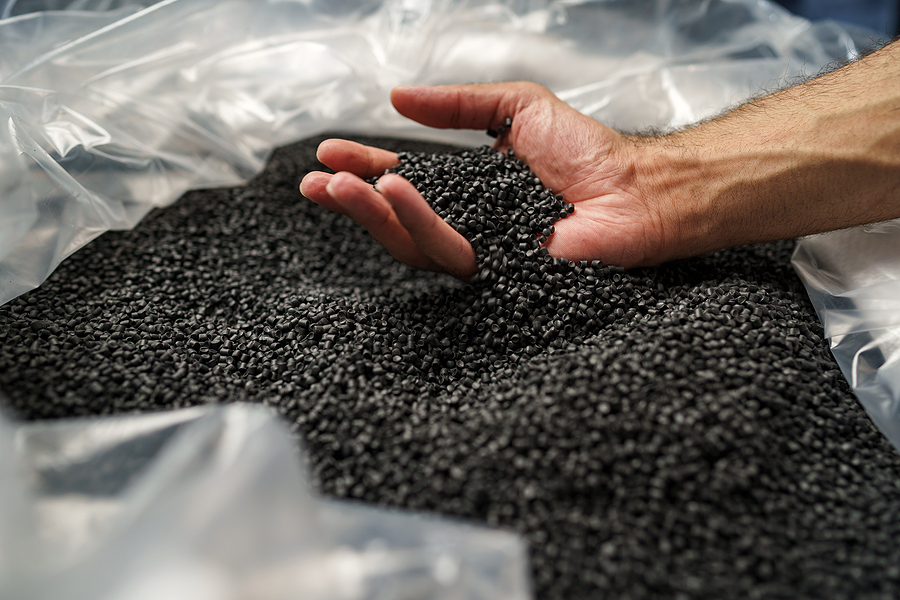
MBA Polymers, UK
In response to heightened interest from the electronics, automotive, and cosmetics industries, a recycled content polymer has been introduced by MBA Polymers, based in the United Kingdom.
MBA Polymers is devoted to transforming Automotive Shredder Residue (ASR) and Waste Electrical and Electronic Equipment (WEEE) from end-of-life vehicles into recycled polymers. Spanning a 13-acre area, this vital operation prevents environmental harm caused by the disposal of waste in landfills or through incineration.
UL Solutions has given its stamp of approval to ABS 4125, which is made up of almost exclusively post-consumer recycled content.
“With manufacturers operating in a market where the demand for recycled ABS outstrips supply, MBA Polymers UK is already exporting its new product to businesses globally including the USA and Hong Kong,” a press release noted.
“100,000 Metric Tons” of Recycled Materials
The press release announced that MBA Polymers UK intends to embark on a mission of supplying 100,000 metric tons of recycled plastic materials to the manufacturing industry by 2030. According to the statement, the firm hopes to achieve this milestone by launching more recycled content polymers in the upcoming years.
Paul Mayhew, general manager of MBA Polymers UK stated, “The arrival of this new UL listed ABS 4125 to the market is a transformational moment and I’ve been excited by the interest it has already created among our customers, new and existing.”
E-Scrap News was informed by a company spokesperson that the recycled content of MBA Polymers’ product, ABS 4125, is achieved through the utilization of more than 27 patented techniques on waste obtained from small domestic appliances, sourced from both the U.K. and the EU.
Mayhew also expressed that many had thought it was impossible to reach such a large degree of recycled content, yet “our team of dedicated engineers and scientists have not only proven them wrong, they have delivered a product, which can turn the growing supply of waste electronics into the next generation of sustainable consumer products.”
Advanced Plastics Recycling
MBA Polymers’ production process begins with EMR Group’s supply of rich, raw plastic feedstock derived from the large shredding and metal recovery operations of end-of-life vehicles and durable goods.
Located in Dover, the team at MBA Polymers’ facility is dedicated to recycling post-industrial plastic materials from the automotive industry. Boasting cutting edge technology, the company’s work involves separating intricate and layered waste streams, including those found inside modern-day vehicles.
By going through its many stages of processing, the company manufactures a recycled polymer that parallels the quality of the initial item. This closes the recycling loop, as large amounts of post-production waste are constantly reused instead of being discarded into landfills.
“Manufacturers know all too well that changes in regulation, consumer behaviour and the impact on the environment, means that increasing recycled content of products and creating circular products is now essential. MBA Polymers UK’s innovative new ABS product helps them to do just that,” Mayhew stated.
MBA Polymers’ Patented Process
To begin, all material is inspected, processed, and divided according to size. This is done to differentiate plastics from other items, including rubber, wood, glass, foam, dirt, and paint. MBA Polymers utilizes a highly advanced separation technology to create a wide variety of polymer grades, including ABS, PP, FPP, HIPS and HDPE.
By applying its unique patented technologies, the company then finishes cleaning and separating the raw materials. Next, MBA Polymers begins formulating, blending, and compounding the granules.
Additionally, every finished product is guaranteed to meet the same high standards as virgin polymer, due to a combination of packaging, certification, and continuous quality checks.
The firm looks forward to its ambitious production goals, continued sustainability efforts, and its success in creating ABS 4125.