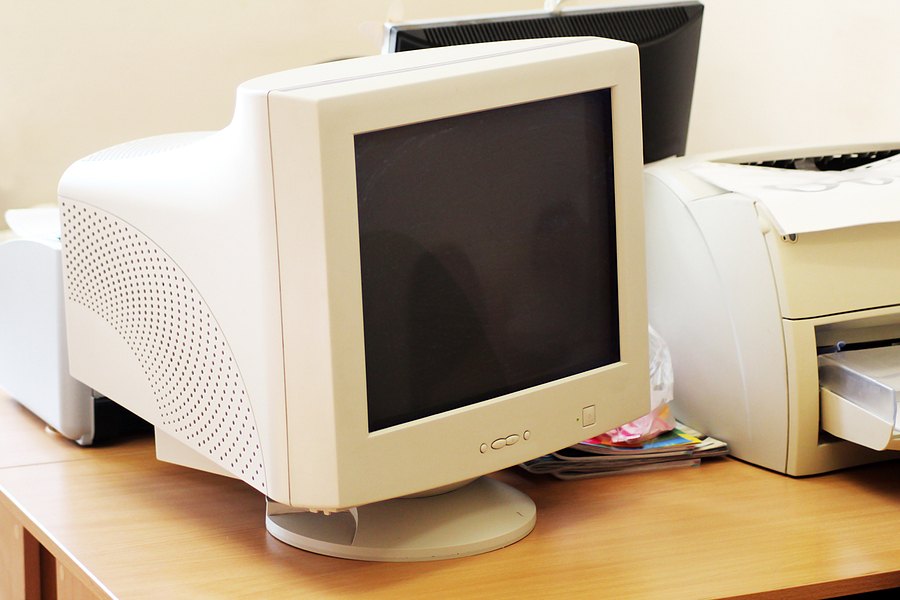
GreenChip Injects Major Capital into Upgrades and Equipment
In the last year and a half, GreenChip has invested millions of dollars in improved machinery for handling CRT glass. According to the company’s managing partner, these upgrades have increased processing capabilities significantly.
“We see the need to supply a long-term solution to our OEM customers and our customers who we are the downstream to,” Bill Monteleone, managing partner at the electronics recycling and reuse firm, emphasized.
Based in Brooklyn, N.Y., GreenChip has recently opened a facility in Fredericksburg, Va.; complete with a large shredder and separator, as well as CRT processing capabilities. In addition to this, the company is taking further steps to build an “eco-campus” at the King George Industrial Park just outside of Fredericksburg.
Historically, GreenChip’s CRT recycling process entailed separating the tubes from the device itself to be sent off to downstream processors like Novotec Recycling. This Columbus, Ohio-based company formerly processed and redistributed CRT materials for smelters, but has since ceased receiving these materials.
Given the lack of clarity within the CRT markets, Monteleone stated “And now, because of that hardship, we said, ‘Let’s come up with a GreenChip solution.”
A Patented System
After GreenChip opened its Fredericksburg plant in 2020, the firm introduced machinery to grind, break, and sieve glass. While keeping proprietary details confidential, Monteleone reported that the system has been running smoothly over the last six to eight months and is able to separate leaded from unleaded segments.
“We had to design this with as close to a zero-stockpile model as we could,” he added.
Drawing knowledge from its corporate parent, Allocco Recycling of New York, GreenChip utilized a processing approach that was informed by Allocco’s years of expertise in recycling large quantities of aggregate. This was highlighted by Monteleone, who formerly held a directorship role in sales at Allocco.
GreenChip had the foresight to construct a “robust” framework with immense processing capabilities, he commented. It can manage more than what GreenChip could acquire in one-day time period. “The equipment is scalable as far as throughput,” he said. “If we’re processing more, we could basically crank it up to output more.”
Monteleone made it clear that GreenChip will not stockpile any CRT materials, something he believes is non-negotiable. “We had to design this with as close to a zero-stockpile model as we could,” he remarked.
To date, the company has allocated “several million dollars” in recent updates to its machinery, for both the CRT glass processing equipment and additional sorting devices utilized along its e-scrap shredding line.
Consistent Downstream Demand
GreenChip is currently undertaking the processing of glass for use by a lead producer, according to company representatives. This extended strategy aids in providing steadiness and security for its clients.
“The idea of looking for a unicorn and being too fancy and being too cute with a solution I feel was maybe the downfall of some of the past solutions,” Monteleone stated. “And we decided to keep it simple and … not over engineering it but relying on the best people in the world who handle lead already.”
Lila Gloyd, GreenChip’s senior vice president of sales and marketing, was adamant that the capacity limitation stemmed from the smelter’s demand. She declared that the smelter can take in an unlimited amount of resources as long as they are delivered in a format the smelter requires.
Though Gloyd was unable to identify precisely which lead producer GreenChip supplies glass to, “they are one of the leading lead recovery operations in the world,” she disclosed, and “they don’t fluctuate in appetite for product.”
“We need to feed the beast, so to speak,” Monteleone said.
He concluded that the need for glass in downstream markets corresponds with the amount available domestically. He saw this as a positive since it meant that the weight of disposed CRT products was diminishing, an outcome he believes is beneficial for all.
Nevertheless, he expressed a strong desire for the final CRT display device to be expediently recycled at a GreenChip facility.
“When everyone’s running away from the CRT stream, we’re walking into it with a fresh mind,” he explained.