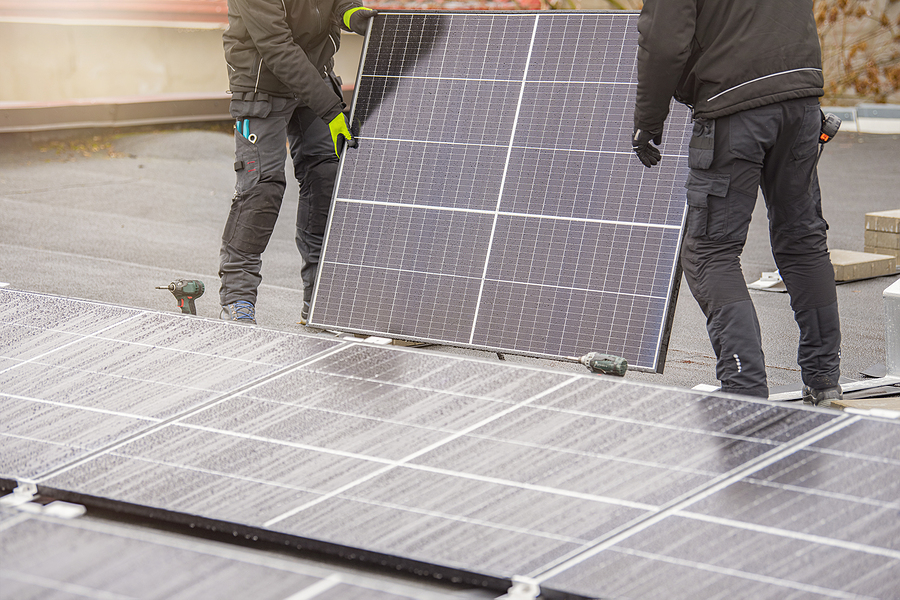
We Recycle Solar
We Recycle Solar, a solar panel recycler based in Arizona, recently upgraded its equipment, and increased its capacity.
With long-term experience in reclaiming assets and recycling electronics, the company has newly applied its knowledge to solar technology. The firm now “acts as a single-source disposal provider for excess, recalled, and end-of-life solar products such as panels, energy storage, and more.”
We Recycle Solar had initially revealed to E-Scrap News that it would be recycling aluminum frameworks, copper wiring, and glass from solar panels using a process involving secondary chemical processing and electrolysis.
Now, the Yuma, Ariz. facility possesses new and improved equipment which has been installed to manufacture glass with lower emissions. Dwight Clark, the director of compliance and recycling technology elaborated on this advancement saying that improvements such as vacuum arms and lifters have been added, making work easier and safer for employees.
“It’s all around recovery of commodity timeframes and getting the glass reasonably clean for some reuse,” Clark stated.
Glass as a Significant Component
Glass comprises a significant proportion of the overall weight of polycrystalline solar panels, traditionally around 70% of the total mass. However, according to Clark, there has been an increased use of biferical panels recently, which consists essentially of two sheets of glass. This has led to a rise in the percentage that glass now accounts for in panel weight, climbing to approximately 85%. As a result, when these modules arrive to be recycled it’s crucial that the glass is recovered.
A feature in Solar Power World has reported that We Recycle Solar’s 75,000-square-foot Yuma facility now boasts an impressive 69 million pounds of processing each year, having the highest processing capacity in the United States. As indicated by the company, this capacity is expected to swell to 522 million pounds per year over the course of the next eight years.
It was also noted that the firm partners with the industry’s “leading utilities, O & M professionals, manufacturers, and contractors in a range of projects from coast to coast.”
Two Different Modes
According to Clark, the facility can run utilizing two different methods – either by processing the frames affixed to the panels or with the frames removed entirely. While a bit more time-consuming, having the frames on greatly increases its operational capacity, despite requiring extra labor at the conclusion of production to isolate the aluminum pieces. With each panel’s weight attributing between 10-15% to the aluminum frames, they do add considerable weight.
Clark also explained that his capability for processing is high, up to several hundred panels can be handled in just one hour.
“To hit my production goal of 10,000 pounds an hour, I run them with frames on, but then there’s an extra step of removing the aluminum later,” he said.
Currently, to reduce long-distance trucking and limit the number of carbon emissions, We Recycle Solar is actively searching for more creative solutions to reuse material. According to Clark, particular attention has focused on states such as Minnesota, New York and Vermont, which have passed legislation that necessitates solar panel recycling.
“The more we can keep out of the landfill, we’re all for that,” he said.