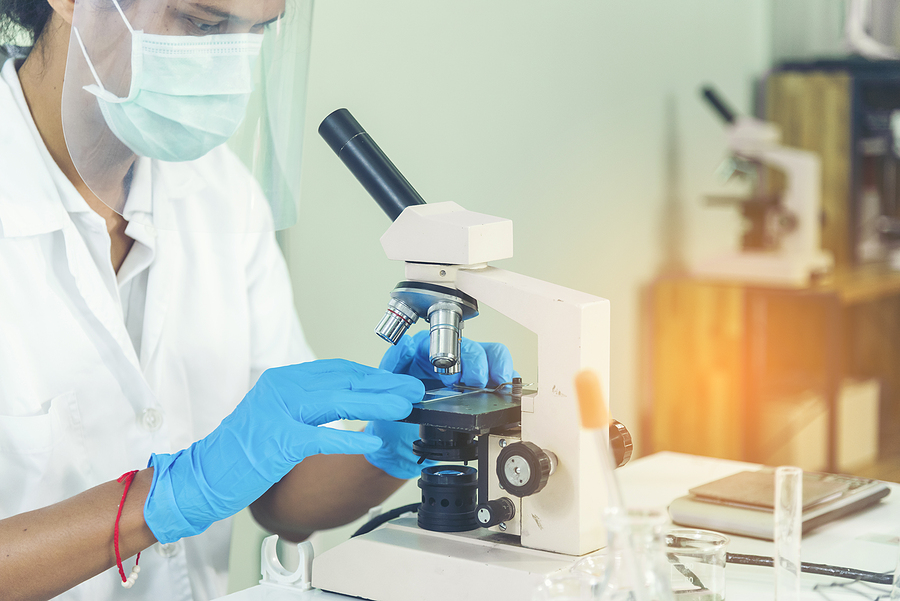
Electric Vehicle (EV) Sales Soar
The International Energy Agency in Paris reported that last year, more than 10 percent of global vehicle sales were Electric Vehicles (EVs), with this figure projected to reach 30 percent by 2030. As a result, the demand for the essential materials used to create EV batteries is set to rise.
Organizations like Redwood Materials and Li-Cycle, are taking steps to construct large-scale recycling centers around North America to manage discarded batteries.
Due to the large quantity of li-ion batteries currently in circulation, recycling firms are beginning to prepare for the influx. Meanwhile, other organizations are attempting to enhance lithium-ion battery design so that the recycling process is less hazardous, and safer for the environment.
The Quick-Release Binder
Researchers at the Lawrence Berkeley National Laboratory in California recently crafted a revolutionary adhesive known as the Quick-Release Binder. This paste-like substance is designed to keep active material particles, within the electrode of a li-ion battery, connected to its contacts.
Different properties allow these binders to be shaped and formed to fit many sizes of batteries. Normally, styrene-butadiene rubber (SBR) or polyvinylidene fluoride (PVDF) are used in the making of these standard binders, often with per- and polyfluoroalkyl substances (PFAS) added.
Gao Liu, head researcher on the binder project and senior scientist at the Berkeley lab explains, “The binder has to be very stable for it to work properly in a battery [and] it also has to be able to hold in the components of a battery almost forever,” he says. “However, the binders that are currently being used can’t be easily recycled due to their chemical makeup.”
A Distinctive Composition
In comparison to conventional binders, what makes Liu’s binder unique is its composition. The researcher’s Quick-Release Binder is crafted with two commercially available polymers, namely, polyacrylic acid (PAA) and polyethyleneimine (PEI). These substances are connected through a bond between PEI’s positively charged nitrogen atoms, and PAA’s negatively charged oxygen atoms.
Berkley explains that by submerging the solid binder material in alkaline water with sodium hydroxide, the sodium ion effectively breaks down the bond between the two polymers. Subsequently, these polymers dissolve into the liquid, which then releases any electrodes held within.
The use of alkaline water is crucial to this process, as it enables the rapid extraction of essential components. Consequently, Liu has reported that approximately 99% of the battery can be successfully recycled with this method.
“Our process allows operators to recover much more than what the standard binders allow,” Liu states.
“You can also recover the copper and aluminum foil, which act as the current collectors in the battery. These materials are typically burned to ash when being recycled because the standard method requires heat to burn off the binder holding everything together.”
Lithium-Sulfur (Li-S) Battery Development
Liu and his team crafted the binder during the development of lithium-sulfur (Li-S) batteries, a possible substitute for li-ion batteries. According to him, Li-S batteries can be made without rare cobalt and have a higher energy density than traditional li-ion varieties.
However, there are still several years until Li-S batteries become commercially viable. This is due to problems related to corrosion caused by electrolytes which are necessary for power storage.
Initially, the Quick-Release Binder was created for Li-S batteries. Yet, after further inspection of the electrode coating process, which was discovered to be incredibly similar to li-ion batteries, the team concluded that the binder could be utilized for both battery types.
Lawrence Berkeley Partners with OnTo Technology
The team has newly partnered with OnTo Technology, a recycler from Oregon, to complete the testing of the binder and introduce it to the market. Steve Sloop, founder of OnTo Technology, declared that they will construct model li-ion batteries using the binder for an in-depth assessment of its advantages and features regarding both practicality and recyclability.
These tests aim to measure the effectiveness of the binder’s performance with batch recycling, as well as identifying any potential issues and costs associated with maintaining the process.
“We plan to do some recycling studies on the binder and show the scalability these could have on the recycling side,” Sloop said.
Sloop explains that the company is currently researching how to handle any waste materials resulting from the battery deconstruction process, such as salts and electrolytes. By effectively dealing with these byproducts, Sloop believes this will aid in maintaining the water resources used for breaking down batteries.
Samples of the binder were sent to OnTo from a team of researchers at Lawrence Berkley, for trial operations on a smaller scale. Moving forward, OnTo, “hopes to find a battery manufacturer to join the pilot and create a larger batch of batteries to scale the process from creation to recycling”.
Given its malleability, the binder proves to be an ideal choice for multiple lithium-ion battery applications, and especially fitting for electric vehicles (EVs).
“Aiming to Improve the Design of Batteries”
Sloop’s partnership seeks to revolutionize the design of batteries by using the binder. By enabling consistency in the production process, manufacturers can easily implement this new technology. Additionally, standardizing battery design would help to provide reliable results during the recycling process.
At this early stage, Liu predicts that it will take two to five years for the binder to be available for commercial use, as the model is currently in preliminary phases of development.
Last year, Call2Recycle, an Atlanta-based consumer battery stewardship and collection program, achieved a record-breaking milestone when they collected 3 million pounds of li-ion batteries. This marked the highest number of li-on batteries recycled through its program to date.
“There’s a lot of value that can be recovered from a battery, however, they are toxic in their current form,” Liu states. “We’re trying to introduce the idea of ‘design for recycling.’ This means that from the very start, we want manufacturers to think about how these batteries can have a smaller environmental footprint and how the material used to make them can be efficiently recovered.”