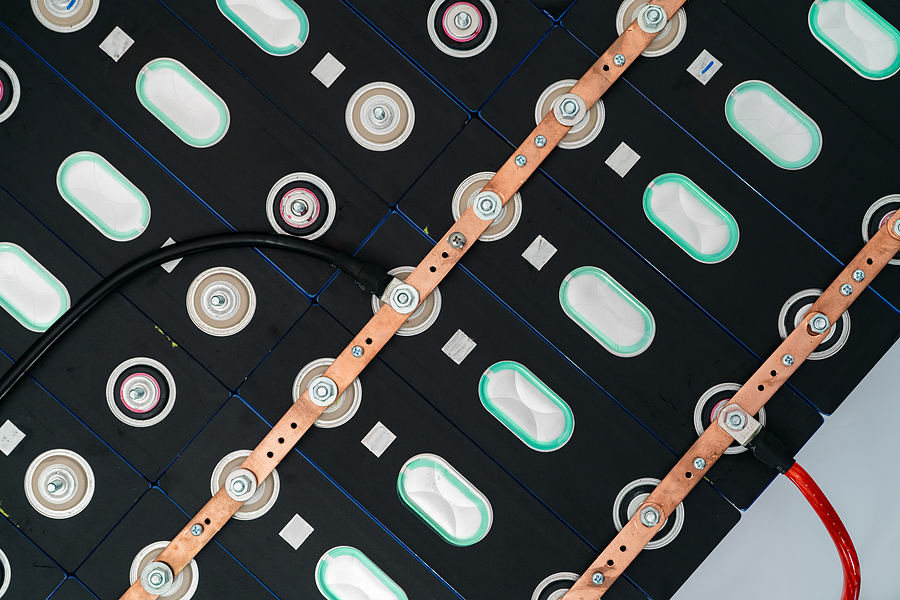
Three Recyclers Release Monumental Announcements
Recently, three organizations have made headway with advancements related to lithium-ion battery recycling. Li-Cycle, AquaMetals, and Ecobat all achieved milestones that are projected to revolutionize the industry.
Li-Cycle was granted federal funding for a new facility, AquaMetals declared an impressive technology breakthrough, and Ecobat presented plans to construct its first site in North America.
Li-Cycle Gains Federal Funding
The U.S. federal government has awarded a conditional loan of $375 million to Li-Cycle, a leading battery recycler, for its latest Rochester, N.Y space that is presently under construction.
By late 2023, it is anticipated that the Rochester Hub will be in service. When functioning at full capacity, this factory will have a production output of 8,500 tons of lithium carbonate, 48,000 tons of nickel sulfate, and 7,500 tons of cobalt sulfate, all sourced from recycled batteries.
Advanced Technology Vehicles Manufacturing (ATVM) Program
Li-Cycle has been given a conditional commitment loan from the U.S. Department of Energy’s Loan Programs Office under its Advanced Technology Vehicles Manufacturing (ATVM) program. According to an official account, this lending “reflects the DOE’s intent to finance the project” but it is subject to fulfillment of long-form agreements and certain conditions.
It was announced in a press release, from its Loan Programs Office, that the conditional commitment had been made for the 12-year loan to close in Q2 2023. This backing is intended for a pure-play lithium-ion battery recycling firm, and marks this program’s fifth critical materials and EV supply chain project of 2022 under ATVM.
Li-Cycle co-founder, president and CEO, Ajay Kochhar, indicated in a press release that the loan “further supports our efforts to create a sustainable domestic supply chain of battery-grade materials.”
In another recent report, members of Responsible Battery Coalition (RBC) praised Li-Cycle for its commitment to sustainability and eco-friendly practices. They noted that that Li-Cycle “lives up to the RBC’s Green Principles by putting the circularity in the circular economy”.
The Responsible Battery Coalition added that this investment should bring lithium-ion battery recycling rates up to match those of lead-acid batteries.
Aqua Metals Unveils Technological Advancement
Aqua Metals publicized that its Li-AquaRefining recycling plant in the Tahoe-Reno Industrial Center has been able to successfully extract high-grade lithium hydroxide from lithium-ion battery black mass.
Steve Cotton, CEO and president of Aqua Metals, confirmed in a press release that he considers “Li AquaRefining is now the only proven battery recycling technology that can produce lithium hydroxide at scale – avoiding the need for additional costly and polluting refinement.”
Further instancing that, “This new capability can have a profound impact on the lithium battery industry in North America”. “Our sustainably recycled lithium can help ensure a robust supply of critical metals to meet the Inflation Reduction Act’s ambitious goals for domestic content.”
The immediate boost in lithium hydroxide production has made it more cost-effective to recycle complex battery chemistries, such as lithium iron phosphate. Due to the technology’s success, Li AquaRefining launched its first pilot scale electro-hydrometallurgy battery recycling plant in North America in 2022.
A Patent-Pending Process
This patent-pending system leverages electricity as a means to recover valuable materials. At its pilot location, it is capable of extracting lithium hydroxide, manganese dioxide, pure cobalt, nickel, and copper metals.
According to a press release, this innovative process “provides the design basis for the company’s 10,000 ton per year lithium battery recycling campus planned for phased development starting later this year.”
Ben Taecker, Aqua Metals’ Chief Engineering and Operations Officer explained that, “Successfully scaling up our unique lithium hydroxide recovery process is a major technical milestone for the industry, heralding an era of low-emissions, circular supply of critical battery metals produced from domestic resources.”
“Producing large quantities of recycled feedstock is new to battery manufacturing, and our ability to combine the recycling and refining of lithium into one process avoids unnecessary waste streams, lowers overall costs and improves supply chain efficiency for the rapidly growing lithium battery industry.”
Ecobat Plans to Build Arizona Facility
An internationally renowned battery recycler, Ecobat, has made the decision to construct its third lithium-ion battery recycling plant in Casa Grande, Arizona. This will be its first facility in North America, and comes as part of the company’s larger plan to expand into the region with its existing anode manufacturing company nearby.
Ecobat currently operates two other lithium-ion recycling plants located in Germany and the United Kingdom.
Construction of the Arizona plant is planned to begin in Q3 2023, with a goal of producing 10,000 tons of recycled material annually. This site has been designed to allow for future expansion and will specialize in sorting, shredding, and separating battery materials for black mass production.
Marcus Randolph, Ecobat’s CEO, said the Arizona location “represents a significant milestone in Ecobat’s strategy to grow our lithium-ion battery recycling business to a scale, similar to our world-leading lead battery recycling business.”
Tevva Unites With Ecobat
Tevva, a prominent UK-based electric vehicle manufacturer, has declared that it will be joining forces with Ecobat to initiate a pilot phase for the restoration, repurposing, and recycling of its lithium-ion batteries. This 12-month trial is set to commence soon, with additional plans of future expansion on the horizon.