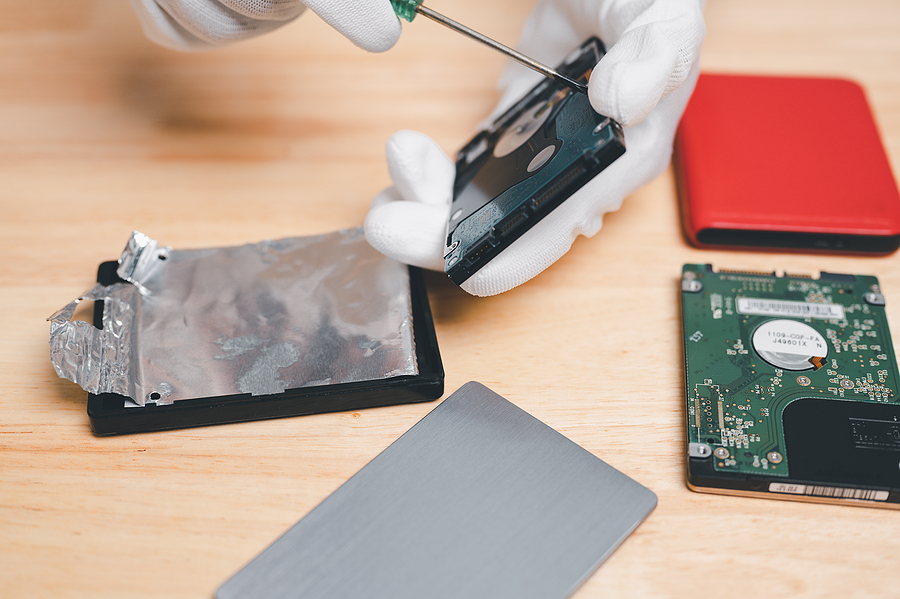
“Recovery as a Service”
It was more than 10 years ago that Greene Lyon Group first established its thermofluid technology to extract chips from circuit boards for reuse. Dale Johnson, CEO of Greene Lyon Group, recollected, “That was back in 2012; there weren’t any chip shortages then.”
The pandemic-fueled disruption of global supply chains created the perfect opportunity to launch Johnson’s new business division, IC Recovery. Established in 2022 and dedicated to harnessing this cutting-edge technology, the new company was created at the ideal time for commercialization, he explained.
As an alternative to conventional chip extraction methods, the business model of “recovery as a service” employed by IC Recovery, allows OEMs and ITAD firms to pay for efficient, gentle removal of higher-value chips from printed circuit boards. Upon completion, these chips are certified fully functional before being returned to clients for reuse, or for resale.
Johnson detailed how his approach creates chips that not only cost less, but also have a significantly reduced environmental impact. Plus, recovered chips can be obtained much faster than creating new ones.
“The two factors that create pain for someone are the cost of the chip and the time that you need to get it, and we can address both of those,” said Johnson, president and CEO of IC Recovery.
How the Technology Functions
Based in Beverly, MA, IC Recovery has a 3,000-square-foot facility in Berlin, CT that houses its light processing and demonstration line. The space serves as the headquarters for the division’s engineering, design, and fabrication partners, according to Johnson.
Utilizing IC Recovery’s unique process, defended by patents, trade secrets, and its signature Chip-Renew method, the company begins by submerging circuit boards in tanks filled with oil. The oil bath is then heated to an adjustable but consistent temperature and does not damage any of the electronic components or absorb impurities, thus allowing for reuse. It is still possible for there to be evaporative losses over time, and when this occurs, the oil inevitably degrades and must shipped out for further processing, Johnson explained.
In a matter of five minutes, the fluid is used to release chips from both sides of boards, he said. Afterwards, employees manually separate chips into three categories: retinning/reballing, testing and certification, or reuse.
Additionally, IC Recovery has found a way to make use of the non-targeted chips that are recycled. Though these stripped boards have little gold content, they can be sent off to a smelter, due to high British Thermal Unit (BTU) content.
Johnson reported that the current beta system used by IC Recovery can process 5,000 boards each month on a single shift. Come February, a gamma system will be put in place to further enhance automation and is set to double current production capacity.
Benefits for Consumers
According to Johnson, IC Recovery had been approached with the task of extracting chips from advanced telecom boards. Such components would have cost roughly between seven and ten thousand dollars to build, and it was estimated that the process would take around six months to complete.
IC Recovery retrieved the chips for the customer at “a really small fraction of the original cost, and we did it within six weeks,” he said.
When it comes to cost effectiveness, IC Recovery puts a focus on more expensive chips like CPUs and GPUs over memory chips, which have less value. To help customers decide between recovering and reuse/resale versus just recycling and buying new, the company has created a cost-price matrix.
Lauren Roman, a business strategy consultant for IC Recovery, highlighted the economic advantages of using the company’s service when larger amounts of the same chip are being dealt with, rather than only a few different types. She made it clear that this could be very beneficial in terms of cost savings.
“If there’s some volume there, then the economics play out,” she commented.
In addition to the financial advantages of reuse, Johnson highlighted the ecological benefits. Analysis conducted by IC Recovery found that chips obtained through his company’s process contained 97% fewer greenhouse gases than newly produced chips. He also noted a Harvard study that discovered “chip manufacturing, as opposed to hardware use and energy consumption, accounts for most of the carbon output attributable to hardware systems.”
“Chips typically have a useful life well beyond that of the equipment they’re originally in,” Johnson stated. “So, disposing of populated circuit boards in the typical fashion of smelting them for precious metals destroys many years of valuable remaining chip life.”
National Security Advantages
Emphasizing the importance of national security, Johnson mentioned that certain pieces of government electronics require legacy chips which are produced outside of the country. This includes older military hardware, which could be at risk due to a lack of control over production.
Last summer, President Biden signed into law Congress’s CHIPS and Science Act of 2022, that included significant financial enticements to encourage domestic production of chips essential for automobiles and defense systems. According to a White House fact sheet, these incentives totaled an impressive $2 billion.
“The equipment that we recover the chips from is already in the U.S.,” Johnson said. “Those chips are already domestically sourced.”
As thermofluid technology expands, ‘recovery as a service’ will only continue to grow across a multitude of industries. The applications for this technology are impressive, with future projections showing great potential.