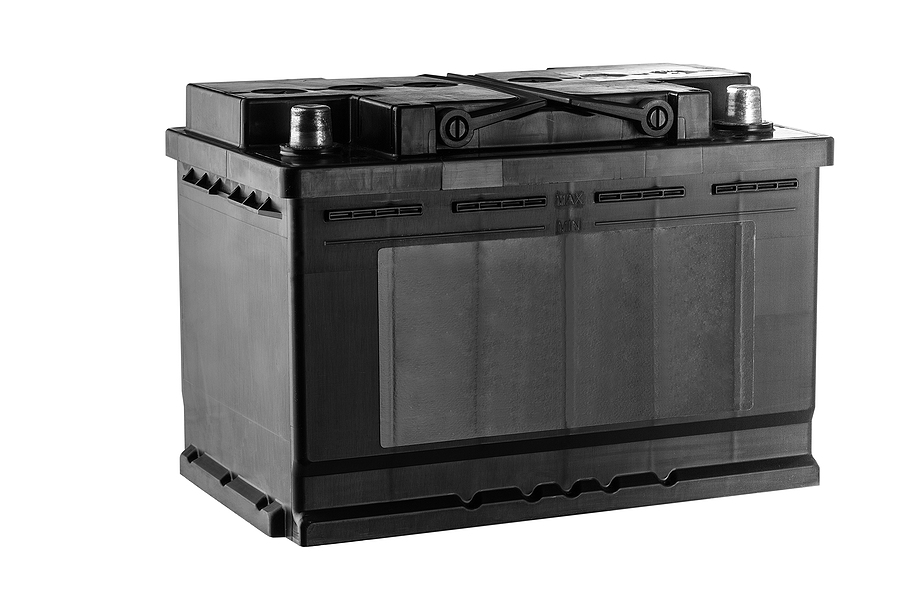
Closed Loop Recycling
An agreement was signed by an electronics recycling corporation based in British Columbia that permits the complete reprocessing of polypropylene from lead batteries. This will allow for the implementation of true closed-loop recycling. The focus of the plastics industry is to become more sustainable. This can be referred to as “closing the loop”, where items are recycled and reused without losing any material. It requires fewer resources and reduces waste significantly.
It is widely known that the green “chasing arrows” symbol on many products signifies that an item can be recycled. Despite popular belief, the chasing arrows symbol does not represent the three R’s (reduce, reuse, and recycle), but instead stands for the closed loop system. Each arrow symbolizes a step in this process:
Collection
To initiate a successful closed-loop recycling system, a key component is the gathering of recyclable products. This can be accomplished through either curbside bins or drop-off centers. Following the collection process, these items are taken to recycling facilities where they are processed and prepared for sale to manufacturers.
Manufacturing
The second stage of a closed loop system is transforming recycled materials into something new and useful. Such products could be a replica of the original item, such as turning plastic bottles into new versions of themselves. Or they might take on an entirely different form, like creating polyester fabric out of recycled plastics.
Purchasing
To complete the cycle, consumers must take part in the third step and buy recycled products. This is known as “closing the loop.” Purchases of goods made from recycled materials are integral to ensuring that recycling efforts are successful.
The process of “closing the loop” offers significant environmental benefits, primarily through lessening the amount of raw materials used and decreasing energy expenditure during manufacturing stages.
East Penn and KC Recycling Collaborate
East Penn Manufacturing, a lead-acid battery manufacturer, and KC Recycling, a CRT device and lead-acid battery recycler, recently joined forces. The two companies established an agreement where KC Recycling would provide East Penn with 100% recycled polypropylene (PP) pellets to mold into new battery casings. PP pellets are obtained from batteries that were initially shipped by East Penn to KC Recycling.
“We recognize that as stewards of the circular economy – even if it’s perhaps not the easiest way to make a buck … – it is the right thing to reclaim the battery plastic and send it to them,” CEO of KC Recycling, Pete Stamper, told E-Scrap News.
British Columbia Funds Project
As a supplier of CRT glass feedstock to Teck Resources smelter, KC Recycling has been at the forefront of lead battery recycling, consisting of 4-5% PP by weight. Last year, KC Recycling was granted funds from the government of British Columbia for a project to install plastic washing, extrusion, and pelletizing equipment. The focus of this venture was to refine Polypropylene (PP) flake into higher quality pellets to be sold in multiple markets.
It wasn’t until March 2022 that the long-awaited production line was finally operational, Stamper commented. Since then, approximately 100,000 pounds of 100% recycled black PP pellets have been shipped out on a weekly basis. Delays in the line were attributed to vaccination and cross-border travel restrictions.
East Penn Expands Production
Headquartered in Pennsylvania, East Penn is broadening its manufacturing output at factories in Iowa and Texas. Established as one of the premier lead-acid battery contributors on the continent, East Penn offers batteries under the Deka brand.
KC Recycling’s chance to expand came when they were asked to provide plastic sourced from batteries to East Penn’s Iowa facility, according to Stamper. It was reported that approximately one-half of the PP pellets produced by KC Recycling are now being shipped off to East Penn’s Iowa factory.
East Penn has made an effort to have its used batteries recycled as efficiently and sustainably as possible. Last year, the company extended its scrap supply reach to include Washington and Oregon. KC Recycling is the only lead-acid battery recycler west of Minneapolis, and north of Los Angeles that receives supply from East Penn’s distribution centers, according to Stamper.
Finding Other Markets and Expanding Supply
To widen its plastics recycling operations, KC recycling has started to provide PP material to a producer of plant pots in Washington state. Additionally, recycled polypropylene is being sold to manufacturers that utilize the material for creating products such as plastic liners and paint buckets.
Aiming to increase scrap sources, KC Recycling is now focusing on items such as car seats and empty paint containers. “In the coming years we expect to double or triple our production by incorporating new post-consumer plastic products such as car seats, paint buckets, and more lead batteries,” according to a press release.
It was determined that around 40% of the material in a typical car seat comes from PP. During testing, KC’s industrial-scale electronics shredder with a specialized magnetic sorting apparatus was utilized. The analysis found that it could successfully separate out the polypropylene from other components of the car seat.
KC has been discussing the possibility of collaborating with ATMO Recycling, a Canadian non-profit organization operating a collection program in Ontario. It has plans to move into British Columbia, which could be beneficial to KC’s supply chain. To make car seat recycling effective, however, additional infeed equipment will have to be installed by KC.
Closed Loop Benefits
Many businesses are seeking to become more environmentally conscious and closed-loop recycling offers significant advantages. This process helps lower the amount of air pollution that results from greenhouse gas emissions, decreases the quantity of raw materials needed for production, ensures non-recyclable items won’t take up space in landfills, and prevents damage to wildlife from occurring.
According to the Environmental Protection Agency (EPA), “Plastic recycling results in significant energy savings compared with production of new plastics using virgin material. Recycling plastic takes 88 percent less energy than making plastic from raw materials.”
In order to maintain a successful closed-loop recycling system, everyone must take part in ensuring that used plastics are kept out of landfills. This includes manufacturers, recyclers, and consumers. These collective efforts, such as East Penn and KC Recycling’s partnership, ensure reclaimed materials from the waste stream are utilized to generate new products, further supporting the circular economy.